How 3D Welding Tables Are Used in Welding Window Frames
- Precision welding table
- Apr 29
- 3 min read
Updated: 5 days ago
In the world of metalworking and welding, precision is paramount. Whether you're creating intricate parts or assembling complex structures, ensuring accuracy in each weld is essential. One of the tools that has revolutionized the way welders approach complex assembly tasks, like window frames, is the 3D welding table. These tables offer unique benefits that make the process of welding window frames more efficient, precise, and easier to handle.

The Role of 3D Welding Tables in the Welding Process
A 3D welding table, also known as a modular welding table, is a versatile, sturdy platform designed for assembly and welding tasks. Unlike traditional flat workbenches, 3D welding tables are equipped with a grid of holes or slots that allow for the placement of clamping systems and fixtures. These adjustable fixtures hold the metal parts securely in place, ensuring that they stay aligned during the welding process. This feature is particularly beneficial when constructing window frames, which require exact measurements and precise angles to fit perfectly into window openings.

Benefits in Welding Window Frames
1. Enhanced Precision and Accuracy:Window frames often consist of multiple components that need to be welded together at specific angles and positions. A slight deviation can result in poor alignment, making it difficult for the frame to fit into its designated space. A 3D welding table provides a customizable fixture system, enabling welders to position the frame’s components at the exact angles required. This significantly reduces the chances of human error and ensures that the window frame is welded to the correct specifications.

2. Increased Efficiency:Traditional welding methods often require manual measurement and adjustment of the frame parts, which can be time-consuming. With the 3D welding table, welders can quickly and accurately set up their frames by adjusting the clamps and fixtures without the need for constant repositioning. This streamlines the entire welding process and reduces the time it takes to produce each window frame. Additionally, many 3D welding tables are designed to support multiple workpieces simultaneously, further increasing productivity.

3. Flexibility and Versatility:Window frames come in various sizes and designs, and a 3D welding table’s modularity makes it ideal for these varying needs. The table’s components can be easily reconfigured to accommodate different frame dimensions or welding requirements. This flexibility is especially useful when working with custom or non-standard window frame designs. By simply rearranging the modular elements of the table, a welder can quickly transition from one frame size to another, enhancing workflow and reducing downtime.

4. Improved Quality Control:Welding window frames demands a high level of quality control to ensure the frame is both structurally sound and aesthetically pleasing. The 3D welding table’s ability to hold the pieces in precise positions reduces the risk of misalignment or distortion during welding. Furthermore, the table allows for easy inspection of the welds and alignment during the process, making it simpler to correct errors before the frame is finished. This leads to higher-quality window frames with fewer defects and rework.
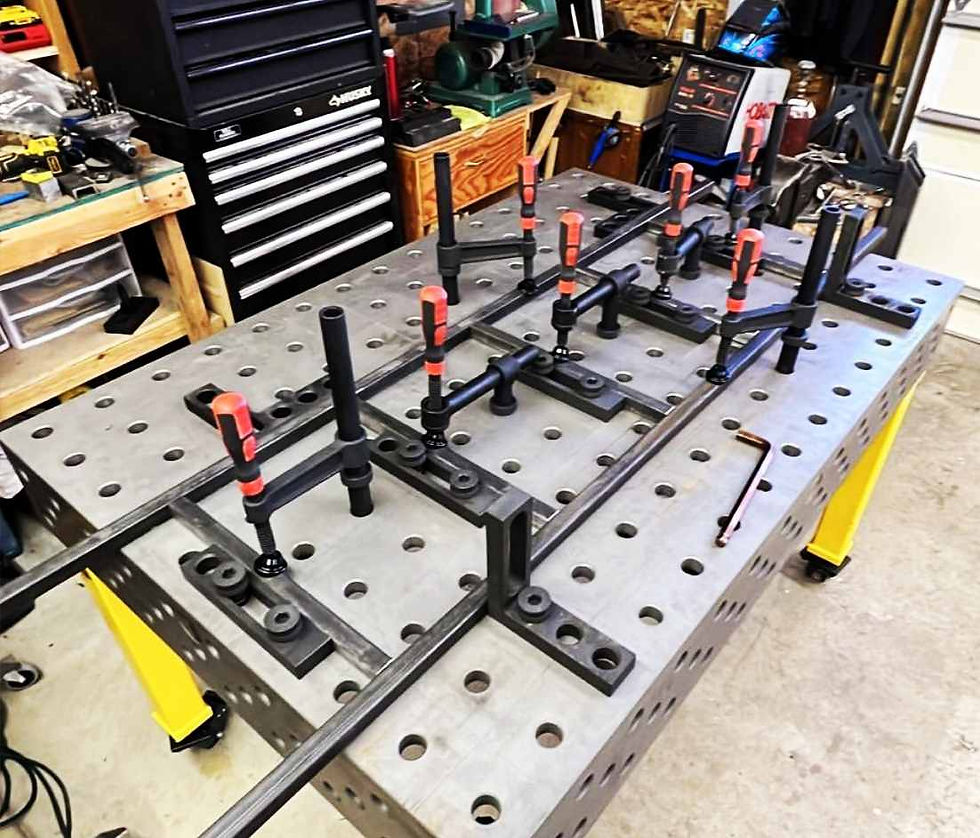
The 3D welding table has become an indispensable tool in the welding industry, particularly when it comes to welding window frames. Its ability to enhance precision, improve efficiency, and provide flexibility makes it an ideal choice for professionals looking to produce high-quality, durable window frames. By holding components securely in place and allowing for precise adjustments, these tables significantly reduce the chances of errors and rework, ensuring that the final product is accurate and well-made. Whether you are working on a small batch or large-scale production, the 3D welding table is a game-changer for the welding of window frames.
Comments